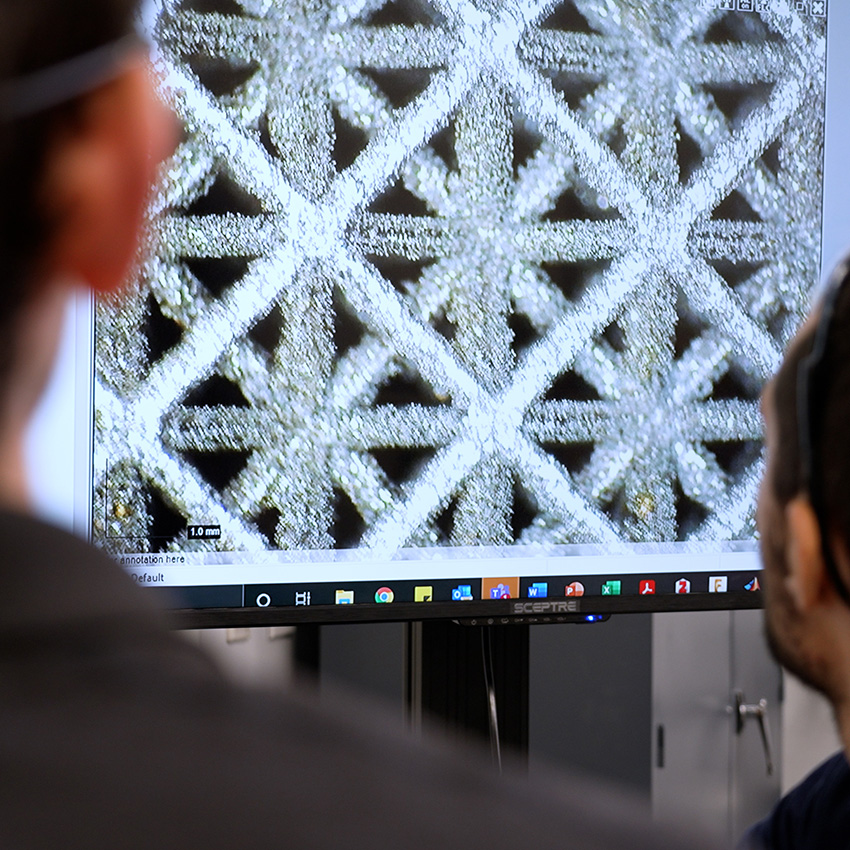
Advanced Manufacturing Systems
GTMI leads pioneering research in advanced manufacturing systems to enhance manufacturing efficiency, accuracy, and sustainability.
Additive Manufacturing
For over two decades, GTMI has partnered with the Georgia Tech Research Institute (GTRI) and faculty from multiple engineering disciplines to spearhead transformative research initiatives in additive manufacturing (AM). These efforts, supported by Manufacturing USA Institutes and various government and industry partners, have positioned Georgia Tech as a leader in advancing manufacturing technologies.
Our vision is to be the premier hub for the comprehensive integration of additive manufacturing (AM) technologies, encompassing product and materials design, process science, supply chain modeling, cybersecurity, and industrial application development. By providing access to cutting-edge research and state-of-the-art software and hardware technologies, we empower both external and internal stakeholders to tackle complex AM challenges, driving innovation and enhancing the impact of manufacturing processes globally.
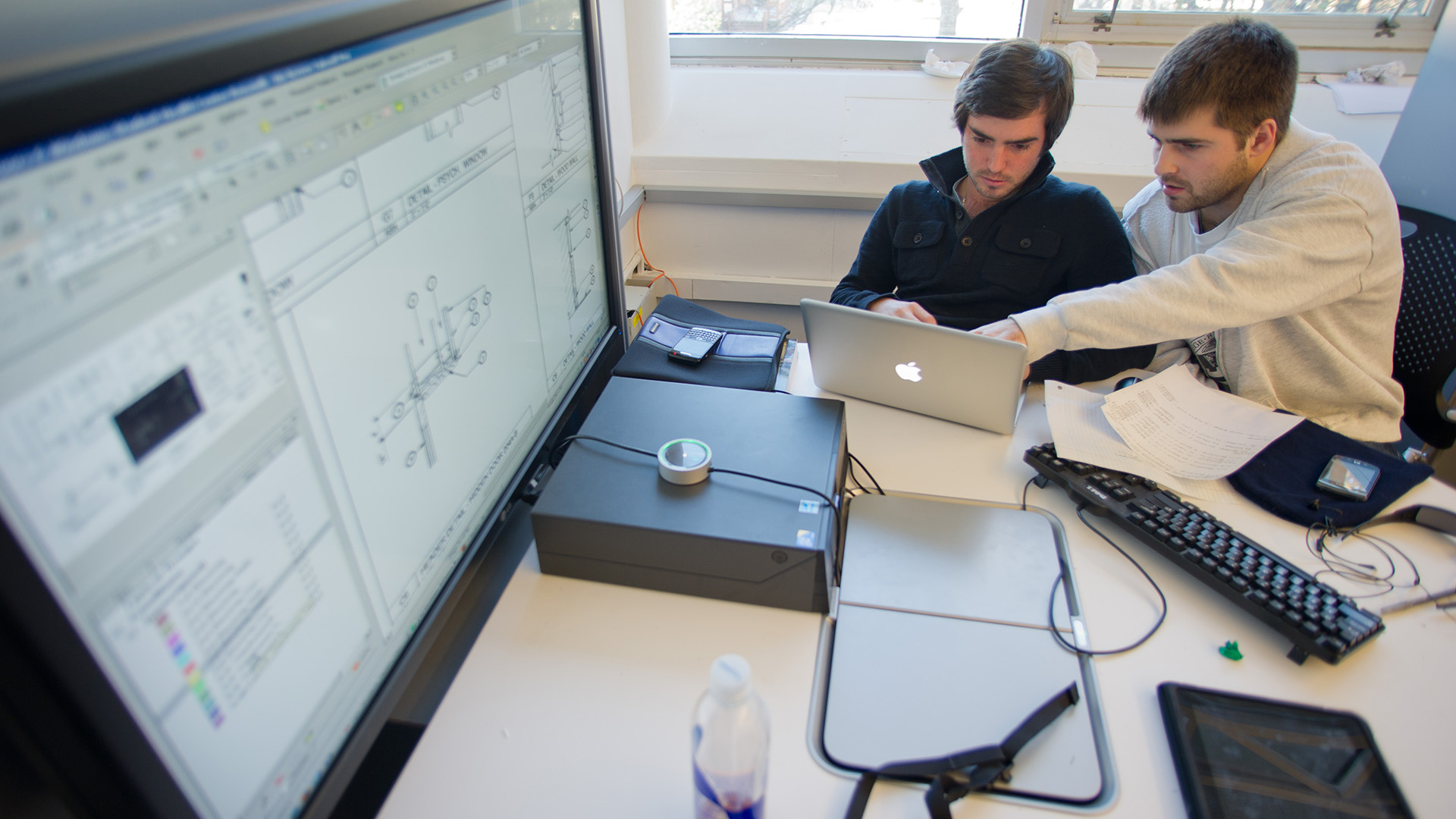
Design for Manufacturing
Design for manufacturing aims to develop tools that help practitioners address AM-specific design challenges for new and legacy products, focusing on minimizing component count while ensuring manufacturability.
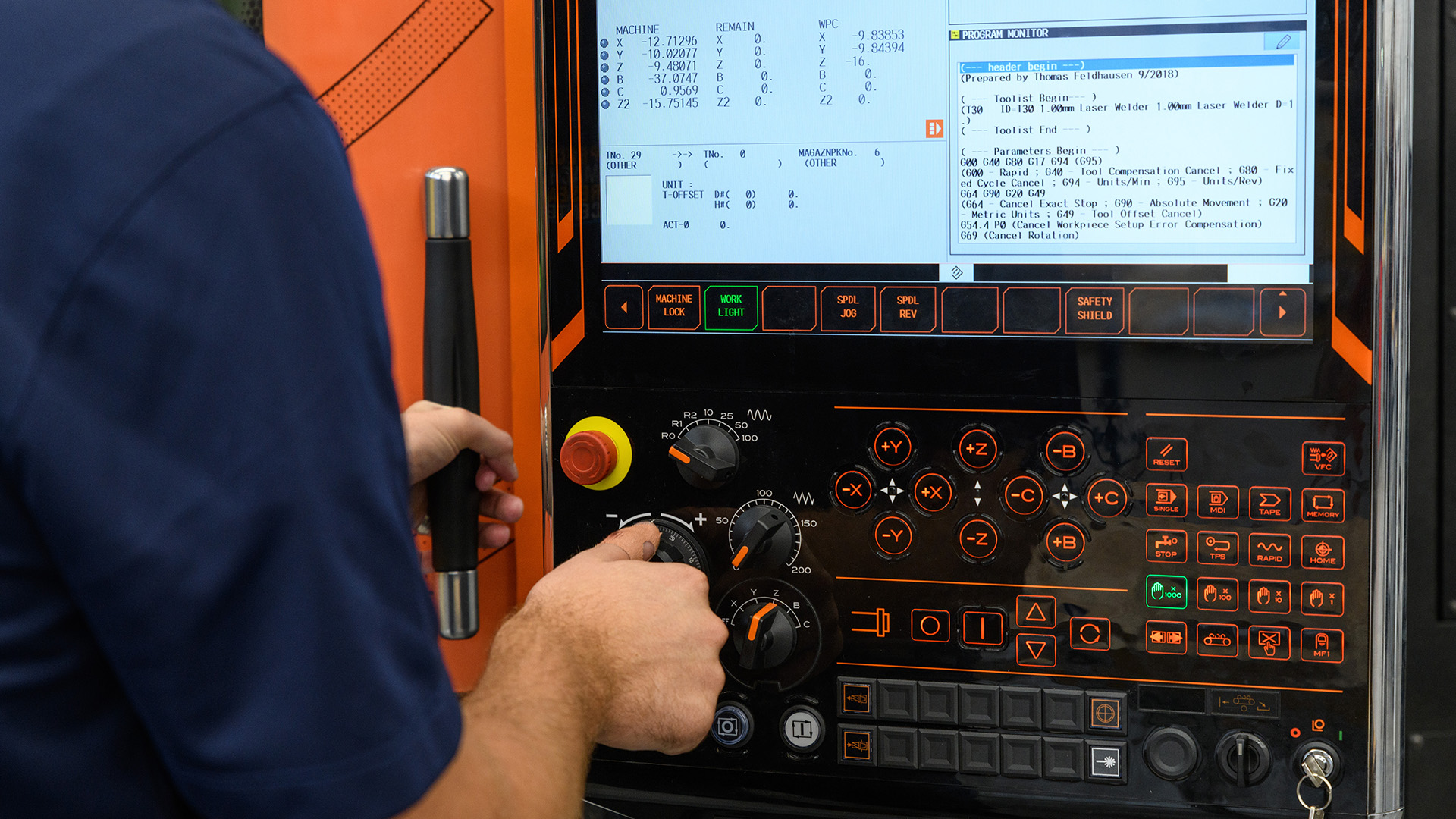
Process Modeling and Planning
Process modeling and planning aims to enable model-based AM process deployment and develop monitoring/control methods for qualified production. It focuses on process monitoring, investigating process-structure-properties relationships, and understanding the impact of downstream manufacturing processes.
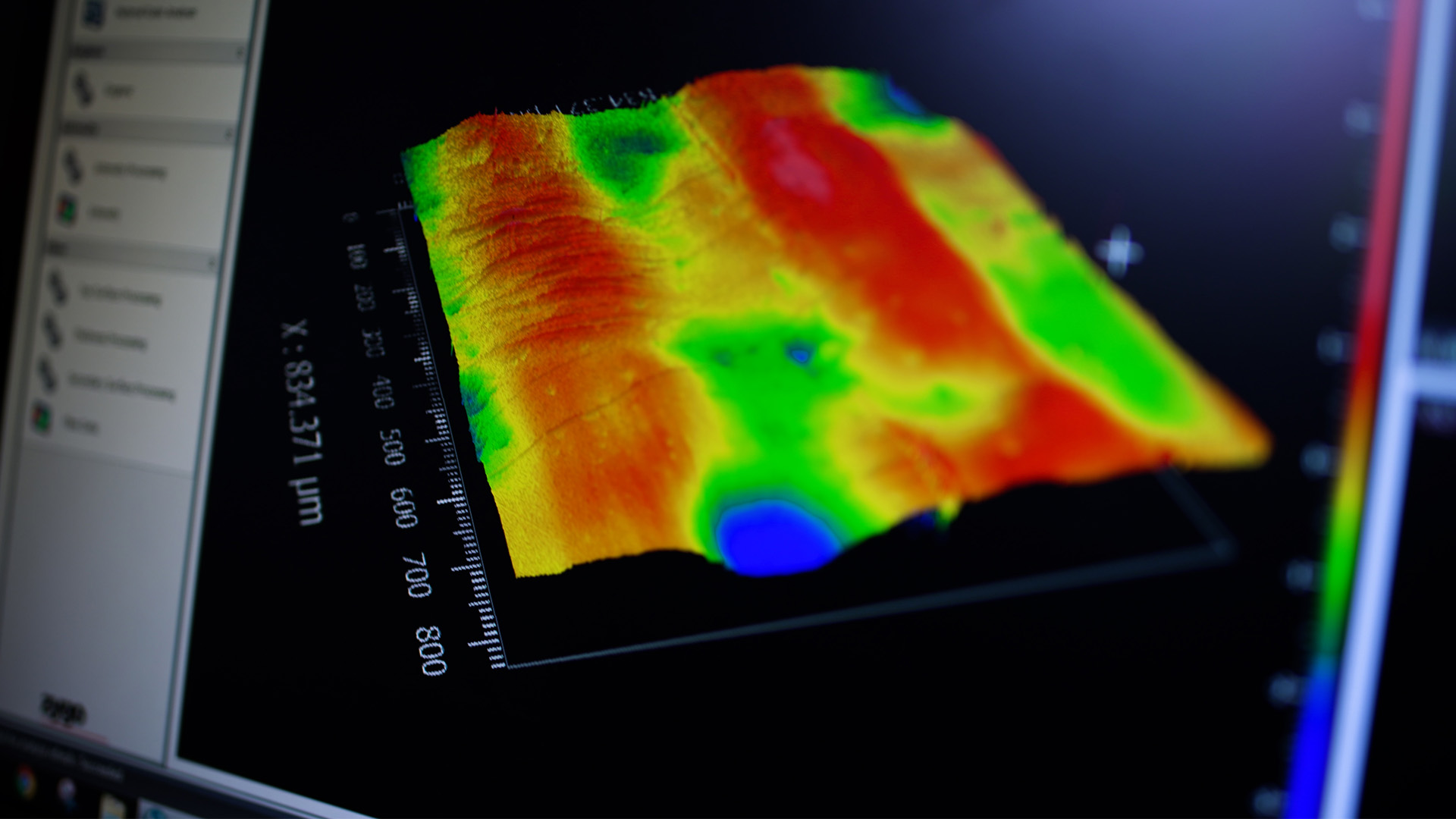
Rapid Materials Screening
Rapid materials screening aims to quickly design, develop, and implement autonomous workflows for exploring and aggregating data-driven knowledge systems. This supports cost-effective, optimized materials-product design for AM components. It focuses on using materials knowledge systems for rapid mapping, establishing testbeds for alloy screening, and supporting materials testing frameworks.
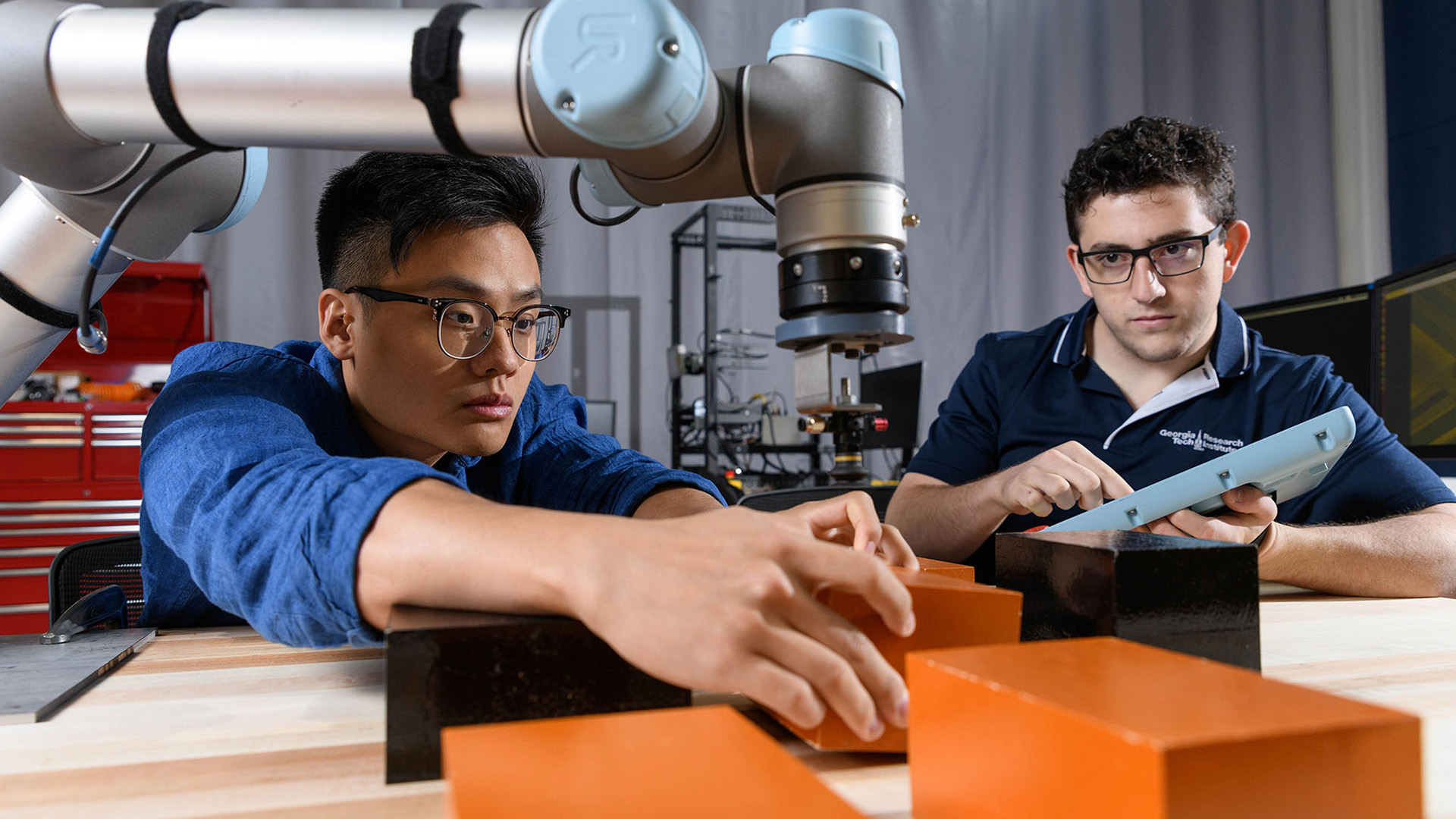
Secure Automation
Secure automation area aims to develop process monitoring and control technologies, along with machine learning frameworks, to support automated and secure AM production. It focuses on creating measurement testbeds for data collection during processing and inspection, and using process/material models for build qualification. Georgia Tech aligns its capabilities with the needs of major industry and government partners, including DoD and DOE, with projects spanning material alloy development, repair processes, materials testing, and applications across multiple industries.
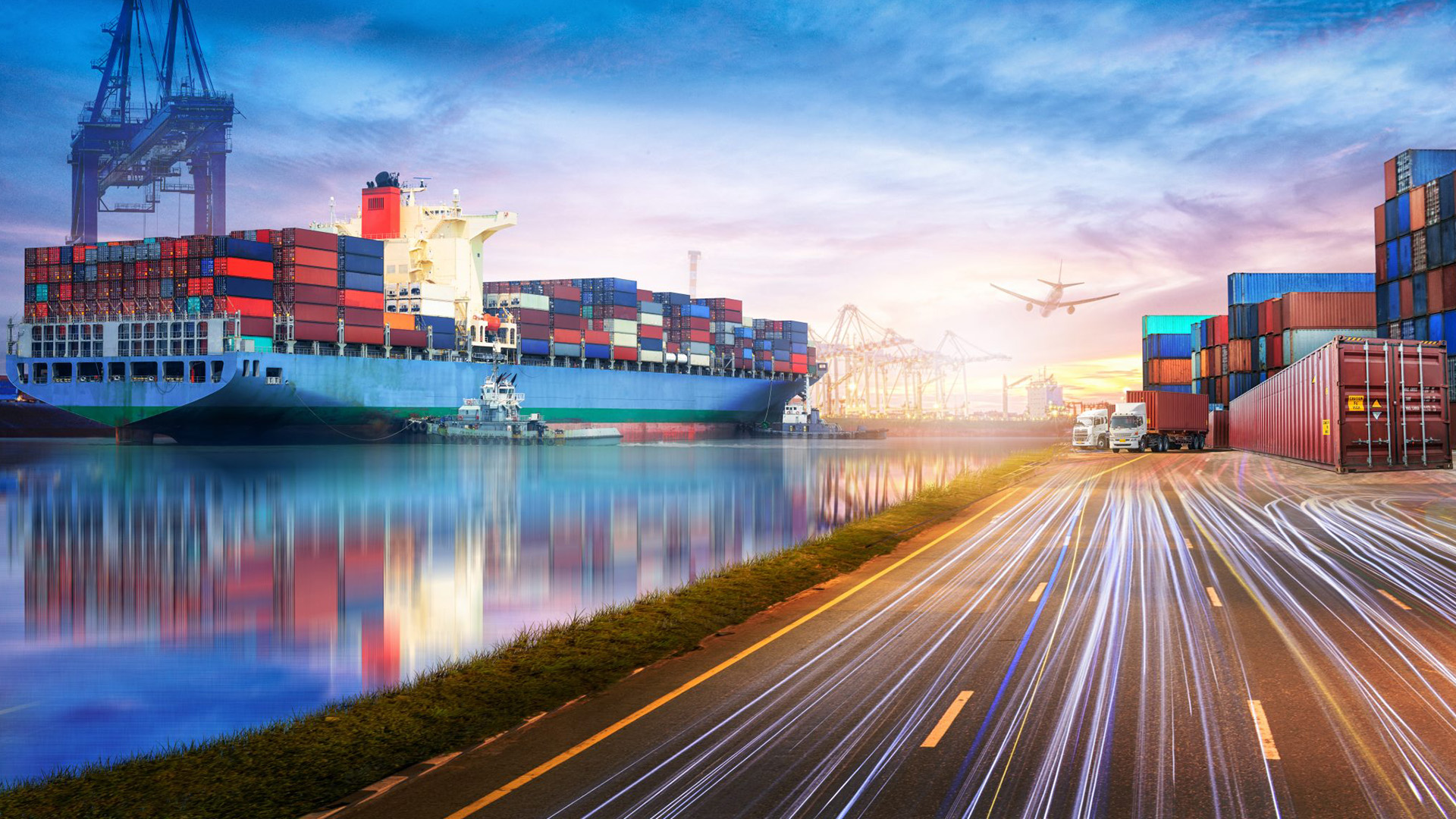
Secure Supply Chain Design
The secure supply chain design area aims to develop data-driven AM supply chains with flexible inventory and manufacturing capacity, combining the benefits of distributed (fast fulfillment) and centralized systems (scalability, risk pooling). It focuses on creating optimal supply chain models and hybrid approaches, and assessing the impact of AM on existing part designs.
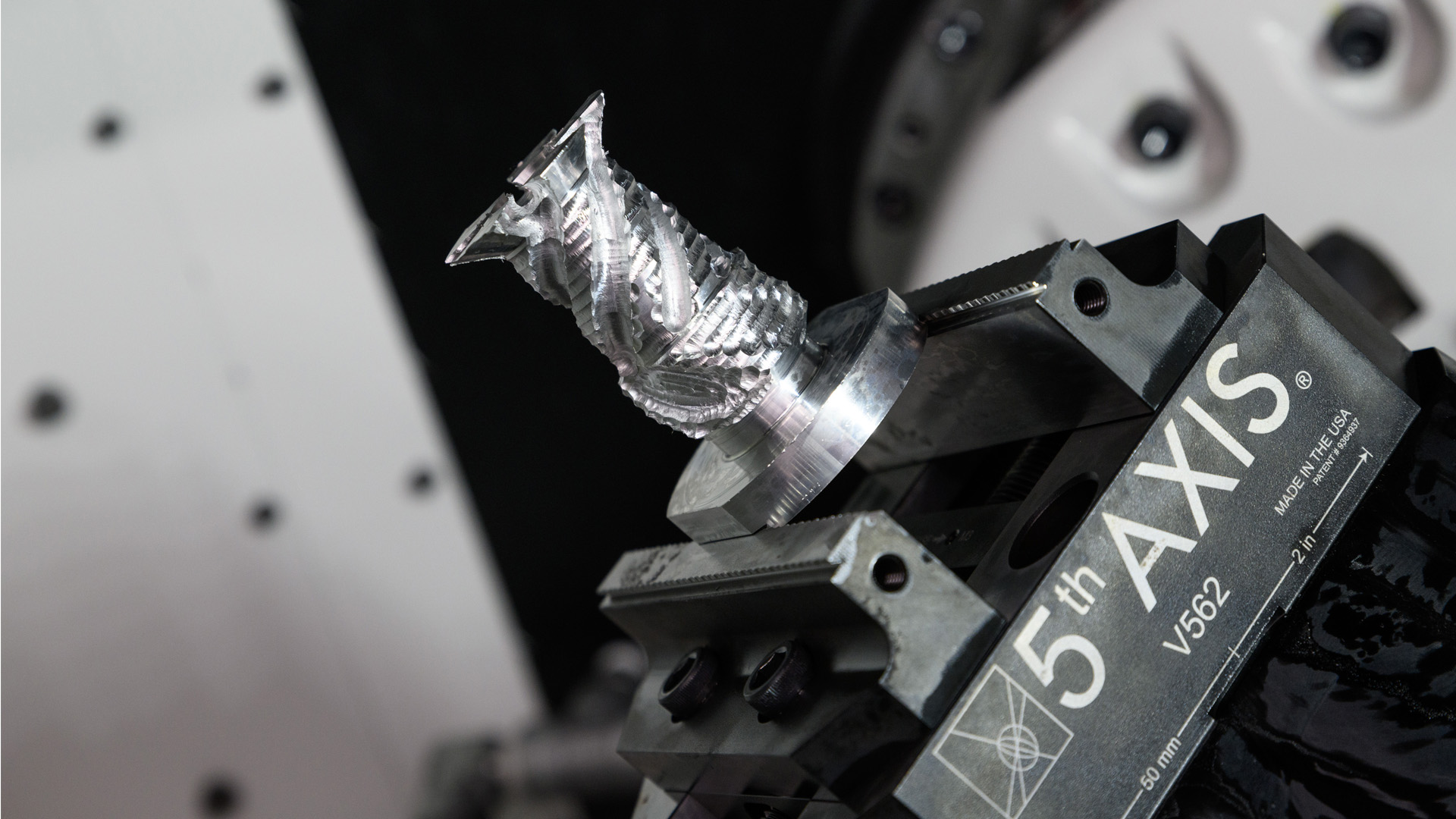
Precision Machining
Precision machining involves the use of advanced technology to produce highly accurate and finely detailed components, essential for industries such as automotive, aerospace, and biomedical. At GTMI, our research in this area is pivotal in advancing manufacturing technologies. Our team, part of the Precision Machining Research Consortium (PMRC), excels in both fundamental and applied research, enhancing efficiency and accuracy in manufacturing.
We focus on areas such as modeling and simulation, digital manufacturing, IoT, machine learning, and process monitoring. Supported by industry and government collaborations, our research drives innovation, ensuring Georgia Tech’s leadership in precision machining.
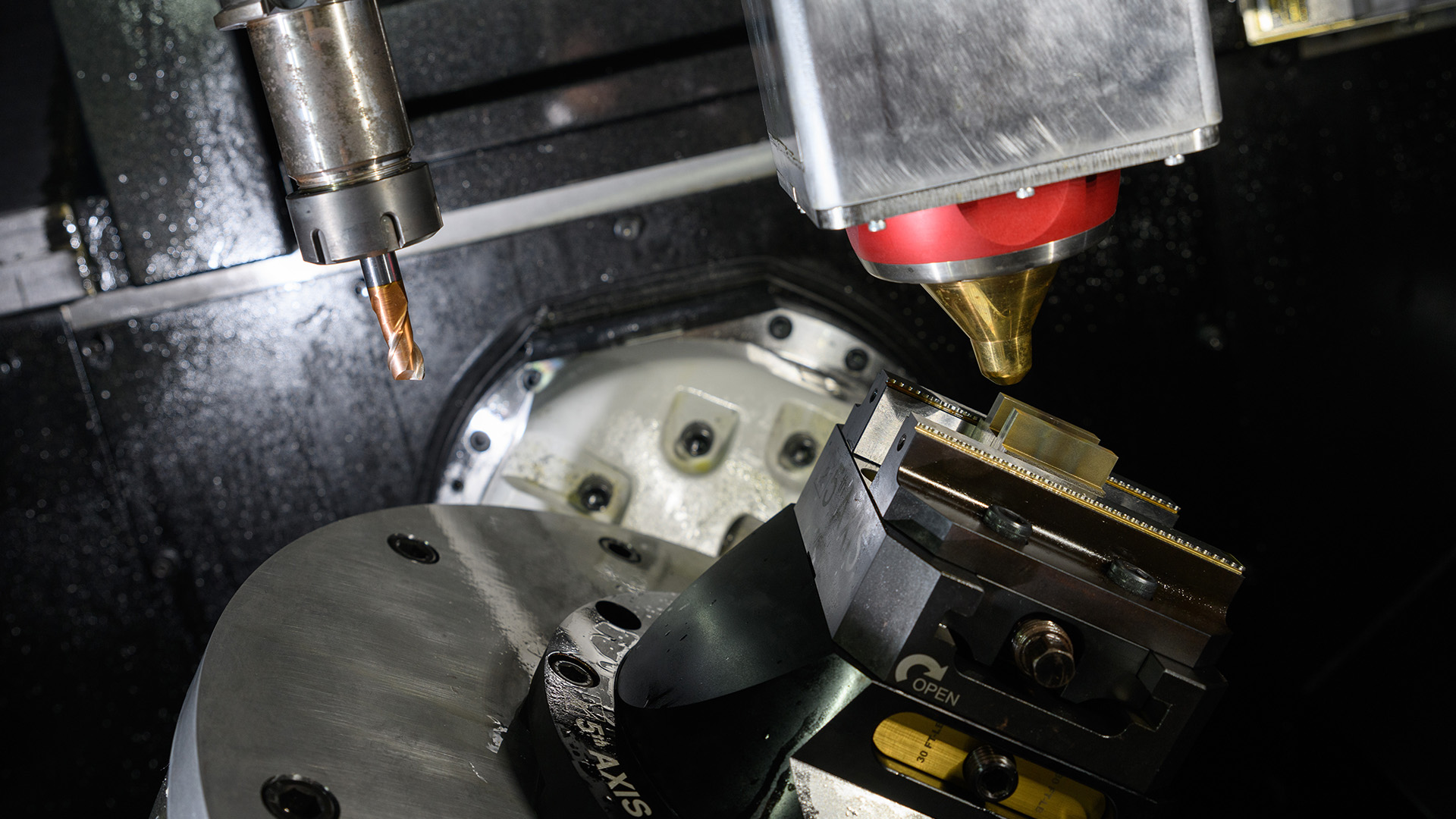
Hybrid Manufacturing
Hybrid manufacturing combines additive and subtractive processes to create complex and high-performance components, enhancing the capabilities of traditional manufacturing methods. At the Georgia Tech Manufacturing Institute (GTMI), our research in hybrid manufacturing is at the cutting edge of this innovative field. Our team integrates these processes to improve efficiency, reduce waste, and enable the production of intricate parts that are otherwise difficult to manufacture.
Our research focuses on the seamless integration of additive manufacturing (3D printing) with precision machining techniques. This includes developing new materials and processes, optimizing hybrid systems, and advancing digital manufacturing technologies. We also explore the use of sensors and IoT for real-time process monitoring and control. Supported by collaborations with industry partners and government agencies, our work in hybrid manufacturing is driving technological advancements and maintaining Georgia Tech’s leadership in the manufacturing sector.
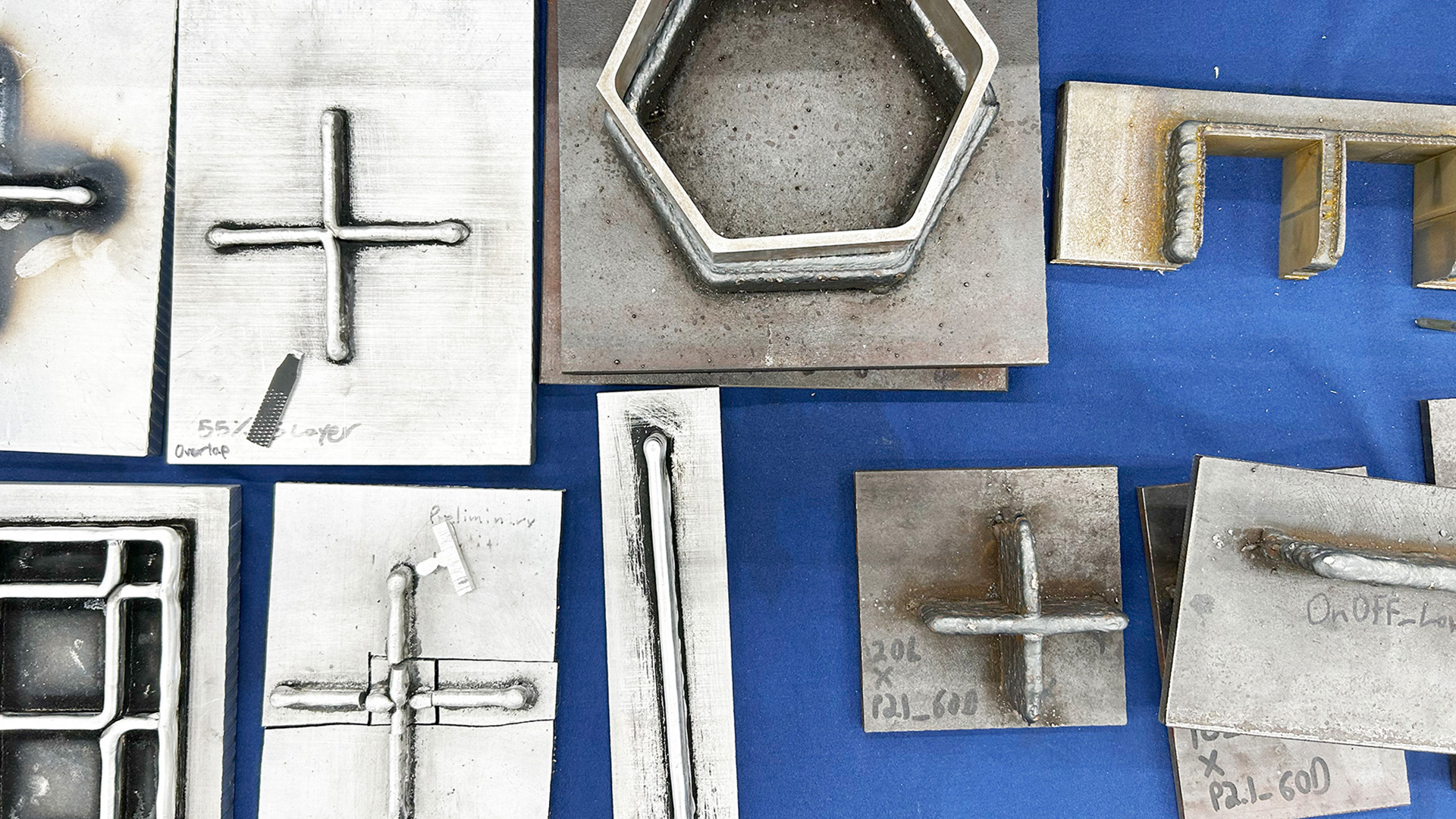
Robotic Welding
Robotic welding is a transformative process that leverages automation to achieve precision, efficiency, and consistency in welding operations. It enhances production speed and quality while addressing challenges like labor shortages and workplace safety. With exceptional capabilities in repetitive tasks, complex geometries, and high-temperature environments, robotic welding is indispensable in industries such as automotive and aerospace.
At GTMI, we are developing advanced robotic welding systems such as Wire Arc Additive Manufacturing that integrate industrial robots with commercial welding technologies to enable high rate joining and additive manufacturing of medium-to-large scale parts. These systems facilitate multi-layer deposition, enabling directed energy deposition-based metal additive manufacturing, which offers significantly faster production compared to traditional methods. We are also developing hybrid robotic systems that integrate additive and subtractive technologies into a versatile hybrid platform for the efficient production of high-quality metallic parts. Furthermore, we incorporate external sensors for advanced defect detection and geometry prediction, utilizing AI/ML-driven techniques to optimize welding and additive manufacturing across various engineering materials.
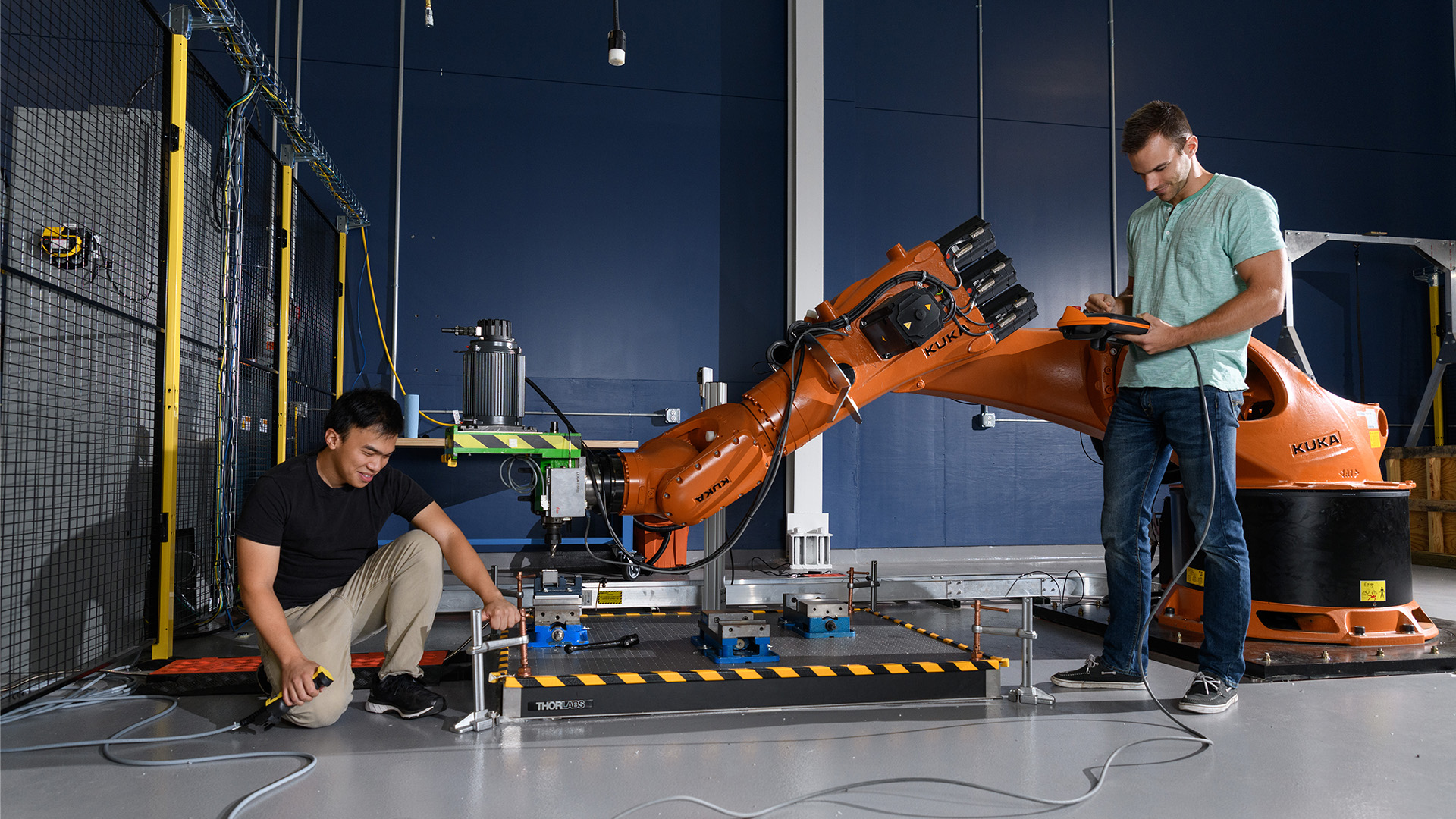
Next-Generation Systems
GTMI is dedicated to advancing intelligent and adaptable next-generation manufacturing technologies. By integrating cutting-edge automation, robotics, AI-driven optimization, and advanced materials, GTMI explores innovative solutions that enhance efficiency, flexibility, and resilience across manufacturing technologies. Key collaborations with manufacturing OEMs, integrators, educators, and end-users enable rapid transition to industry, fostering economic growth and global competitiveness in modern manufacturing.
Monitoring and Metrology
GTMI’s research in monitoring and metrology is at the forefront of enabling intelligent, data-driven manufacturing. By leveraging the Internet of Things for Manufacturing (IoTfM) and the Factory Information Systems Center (FIS), we develop and integrate advanced sensing technologies that provide real-time insights into production processes—ensuring quality, reliability, and efficiency from start to finish.
Our interdisciplinary teams design novel monitoring systems and also adapt commercial off-the-shelf (COTS) technologies into customized solutions tailored to the unique challenges of modern manufacturing environments. These systems support in-situ process monitoring, high-resolution metrology, and data-driven diagnostics that power predictive maintenance, adaptive control, and closed-loop manufacturing.
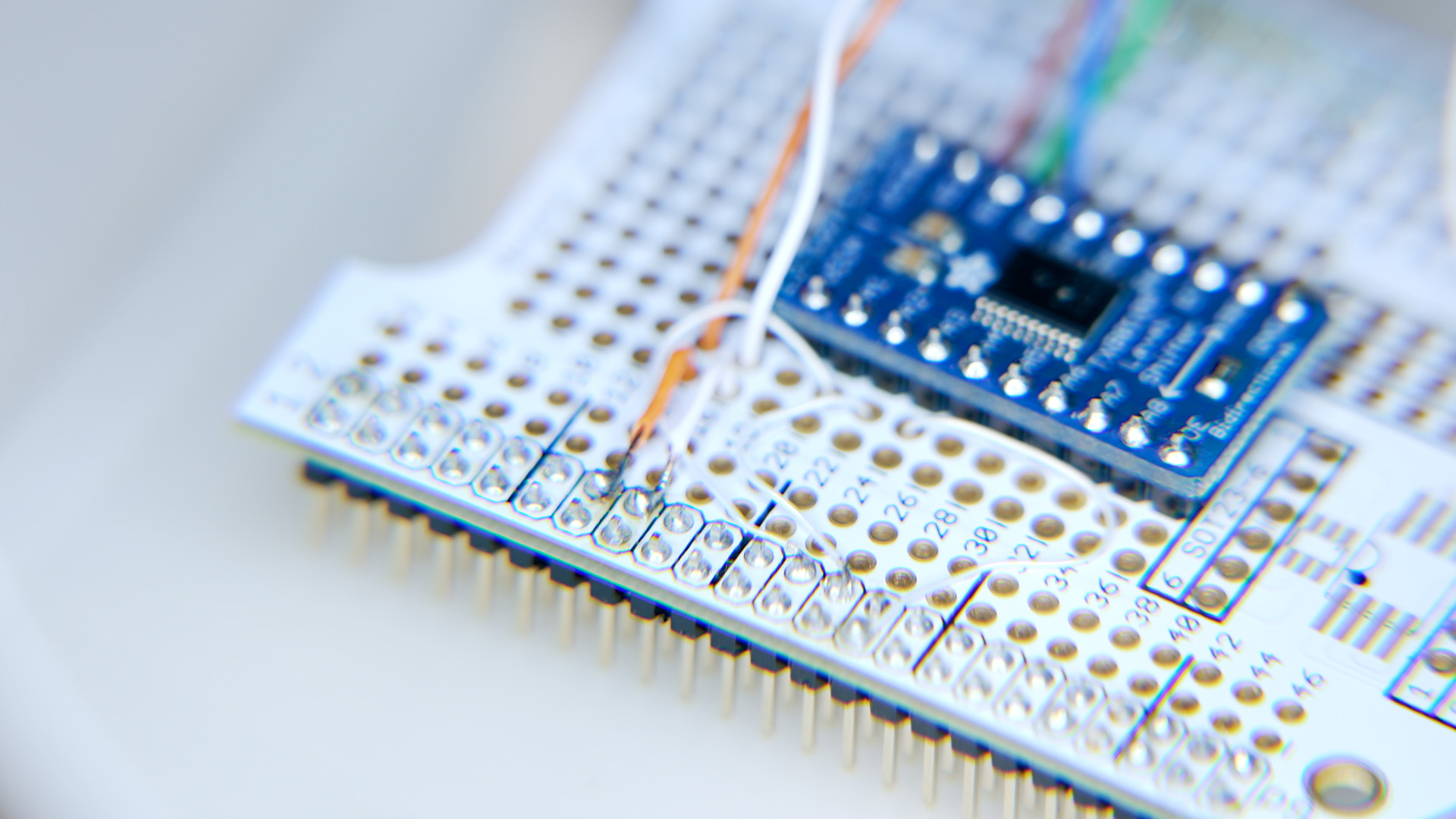
In-Situ Monitoring
In-Situ Monitoring in manufacturing involves real-time data collection and analysis from production processes, equipment, and materials. This technique helps identify inefficiencies, detect anomalies, and improve product quality, enabling proactive decision-making and optimizing operations.
GTMI is advancing these techniques by integrating real-time monitoring into various manufacturing processes. Examples of our projects include optimizing composite material curing cycles and using acoustic techniques for semiconductor manufacturing, which enhance efficiency, reduce risks, and improve overall process control.
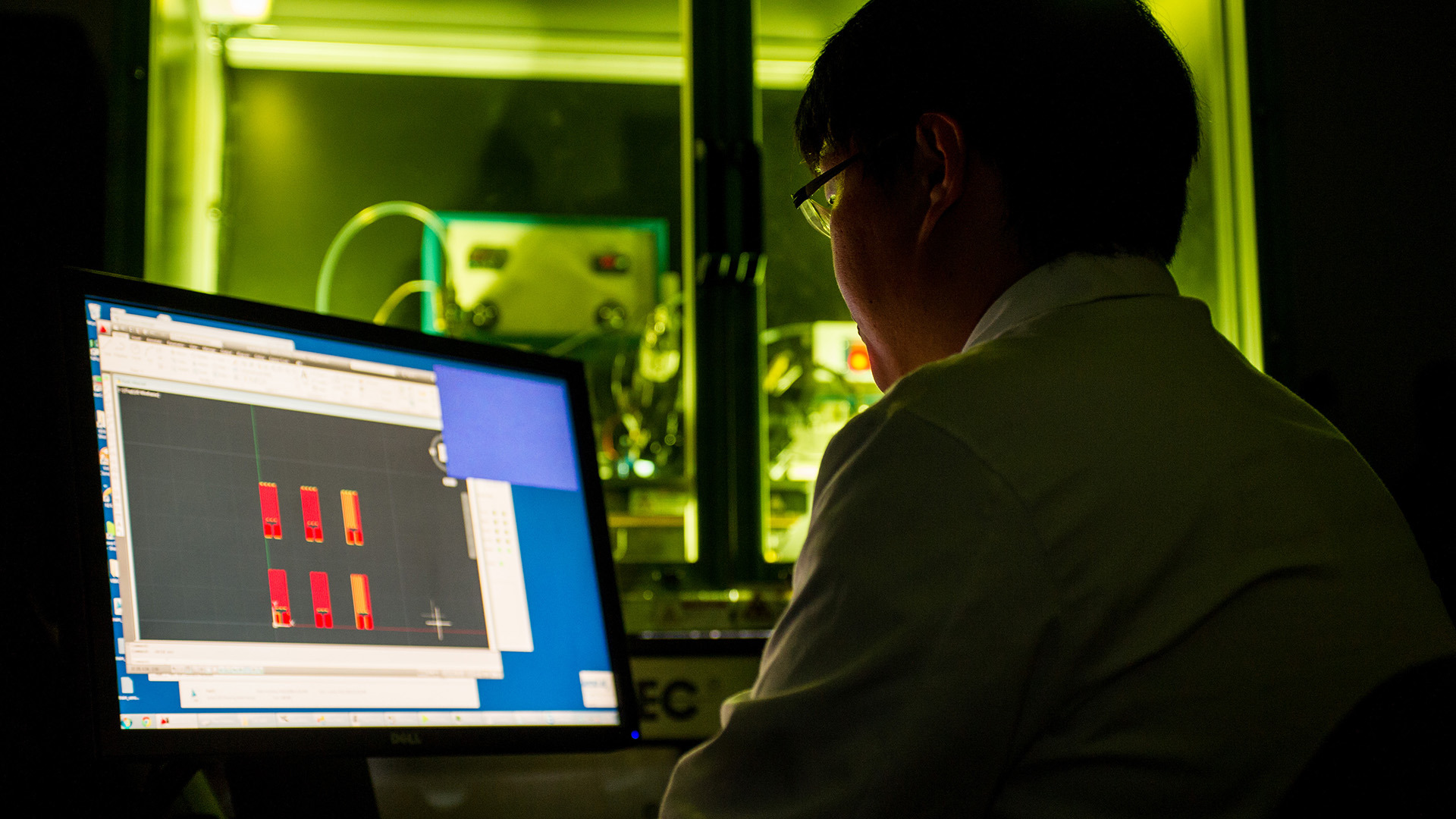
Sensing and Metrology
GTMI is at the forefront of sensing and metrology for manufacturing processes. GTMI’s capabilities enable precise measurement, detection, and analysis of physical and chemical properties for manufacturing technology. Our characterization facility retains world-class, NIST-traceable measurement, characterization, and inspection systems for rapid measurements. GTMI has a long history of developing novel sensing methods for in-situ measurement of manufacturing processes, enabling real-time quality control.