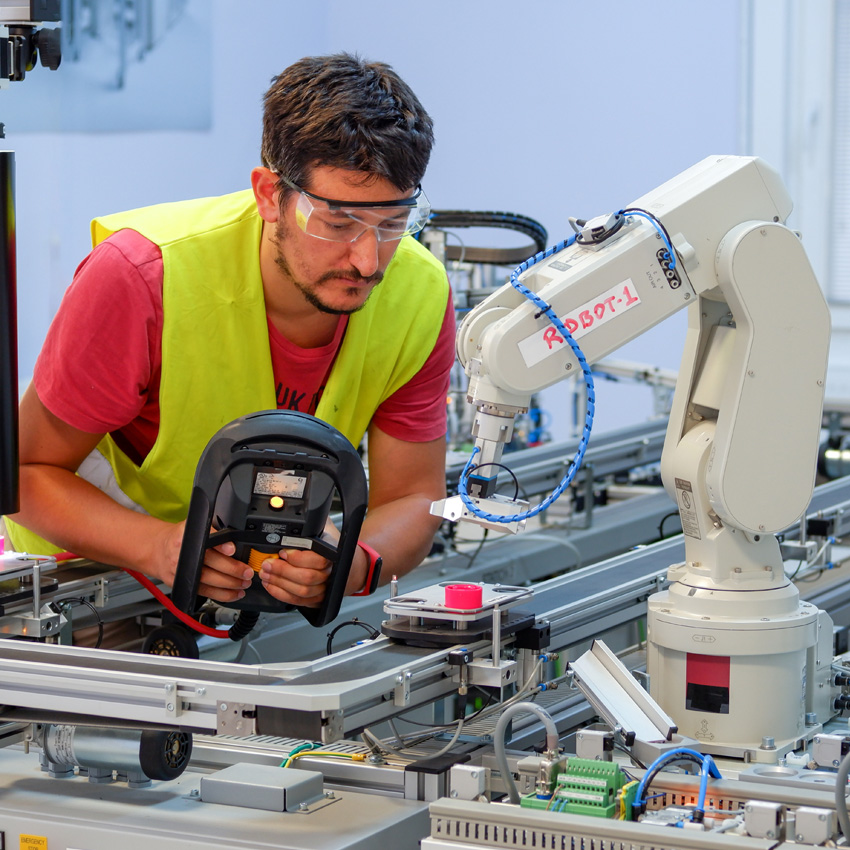
DIGITAL CAPABILITIES
GTMI’s digital manufacturing capabilities bridge the physical and digital worlds, enabling smarter, faster, and more resilient production systems. From factory information systems and machine learning to secure data integration and extended reality, we empower innovation through intelligent connectivity, automation, and real-time decision-making.
Factory Information Systems (FIS) Center
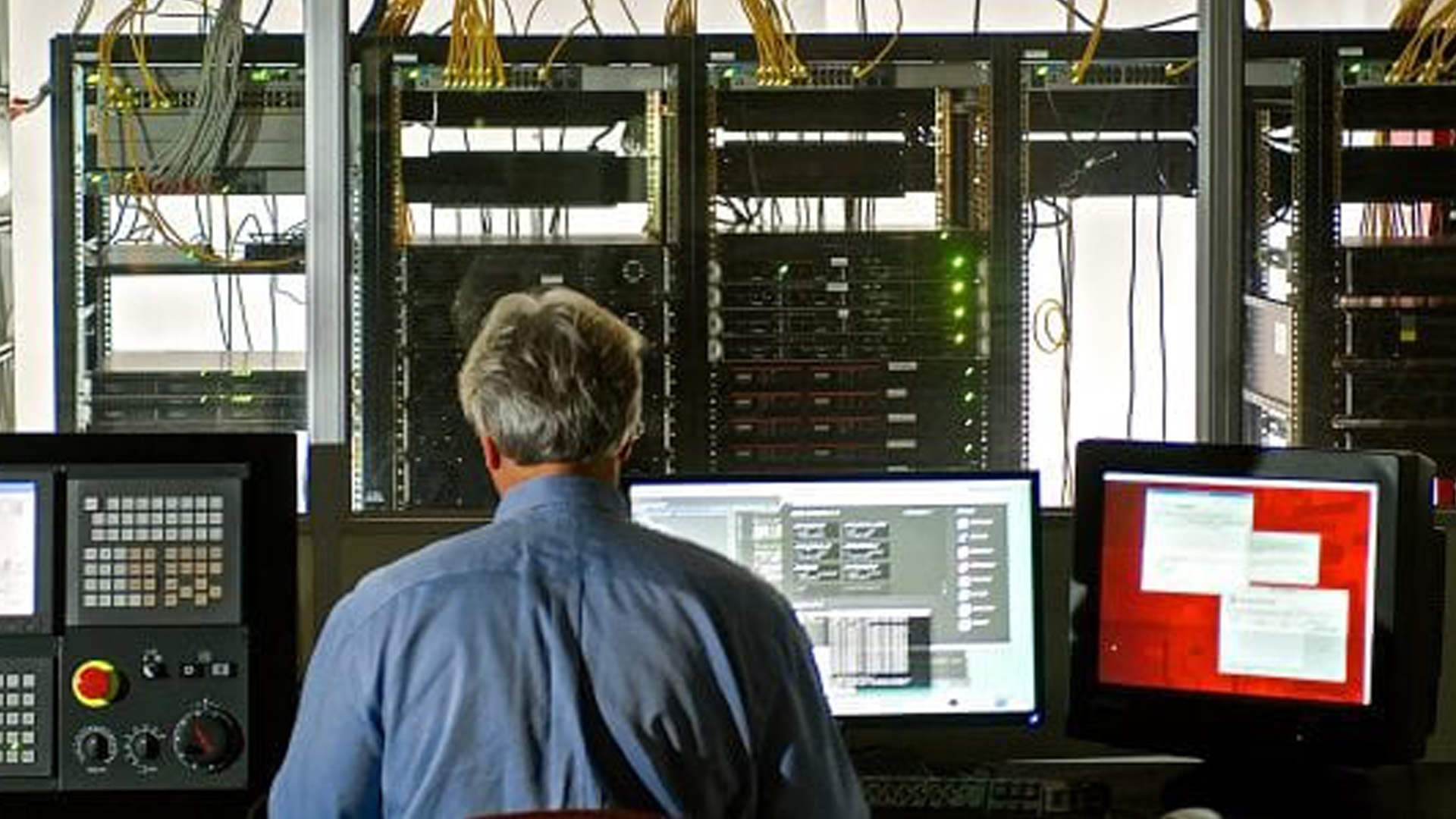
The FIS Center at GTMI focuses on applying emerging technologies to real-world manufacturing problems, helping companies improve productivity and decrease costs. Our areas of expertise include factory architecture, machine communication, cloud computing, machine learning, artificial intelligence, and predictive maintenance. By partnering with the FIS Center, we ensure that our digital capabilities are at the forefront of innovation, providing our clients with the tools they need to succeed in a competitive market.
Main Capabilities:
- Decoupled Digital Architecture for seamless data exchange across machines and applications
- Cloud computing solutions for machine learning, IoT, stream analytics, and high-speed data processing
- Development and deployment of edge devices for high-speed sensor data gathering
- Machine learning and artificial intelligence for process optimization and problem-solving
- Predictive maintenance to reduce downtime, cost, and risk
- Overall equipment effectiveness (OEE) analysis for benchmarking and decision-making
- Cybersecurity research to enhance the security and resilience of manufacturing systems
Data Management
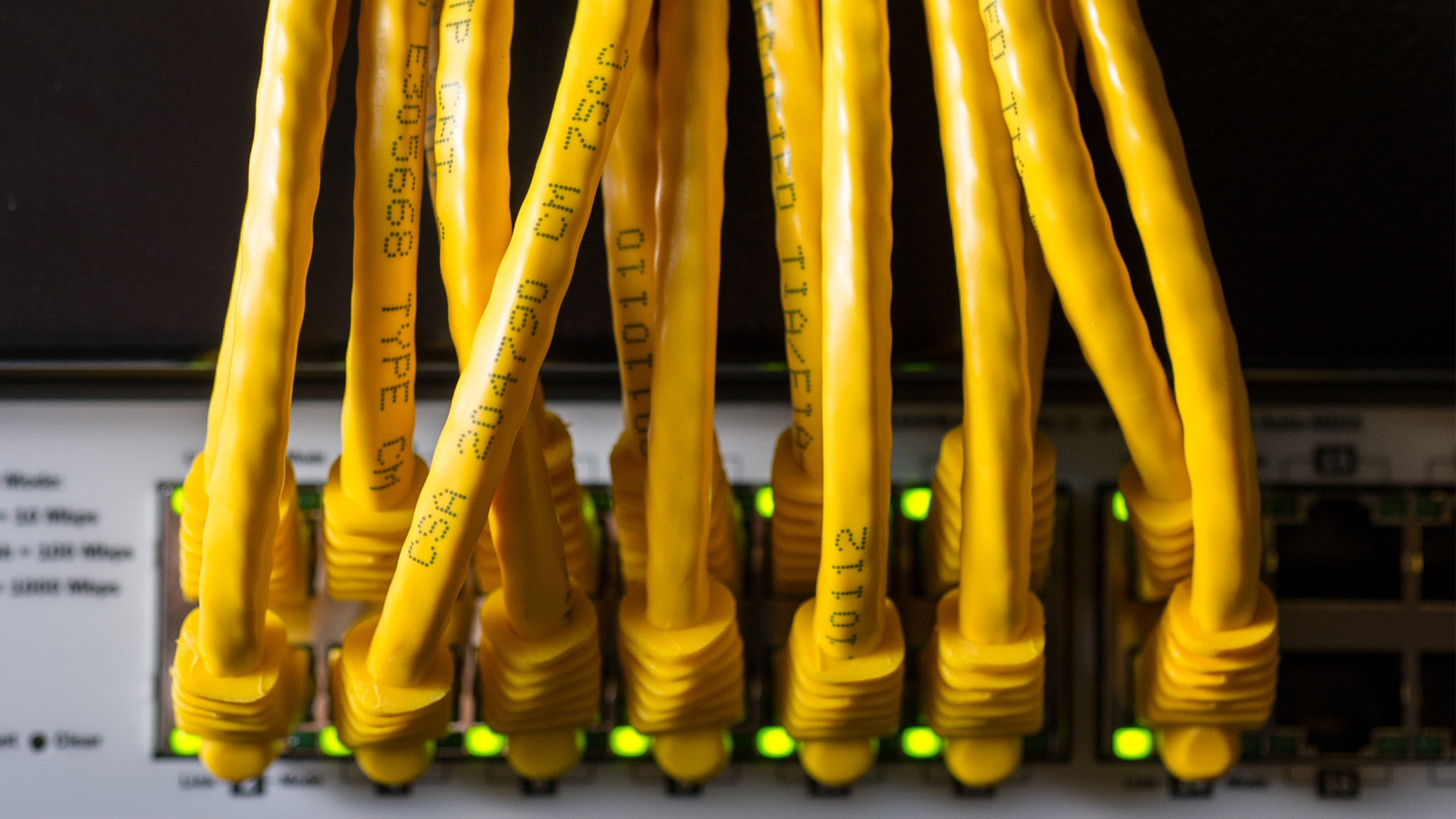
Coming Soon to GTMI
Managing data from various equipment can be challenging due to differences in data collection methods and formatting. At AMPF, we are developing a seamless data management system to integrate and connect these diverse data sources. Our enterprise data management architecture will ensure efficient and secure handling of data, enabling informed decision-making and streamlined operations.
Main Capabilities:
- Equipment integration via protocol normalization and standardized data structures through the Decoupled Architecture
- Curated data storage and retrieval to support experimental effectiveness
- Multi-site material routing, processing, and traceability
- Advanced analytics and reporting
Data Communication
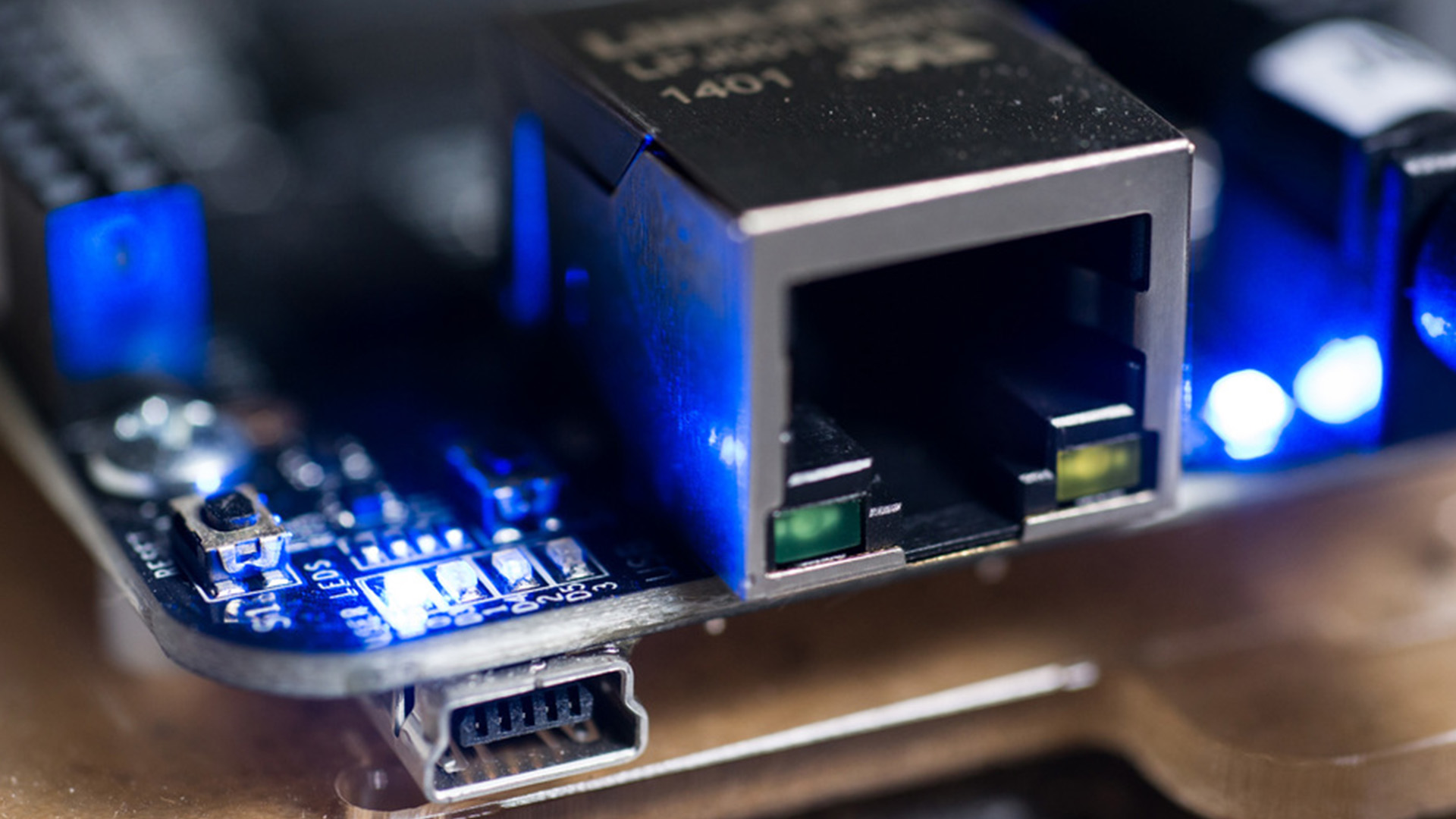
GTMI is a leader in streamlining communication with machines on the shop floor. We develop solutions that address the wide variety of protocols used by manufacturing equipment, PLCs, SCADA applications, MES, and ERP systems. Our capabilities in 5G and millimeter wave (mmWave) technology provide high-speed, reliable communication essential for modern manufacturing environments. The Factory Information Systems (FIS) Center at GTMI plays a crucial role in developing and implementing these technologies, enhancing our communication infrastructure.
Main Capabilities:
- Enhanced network reliability and security
- Streamlined machine communication protocols, including OPC-UA, Modbus, ROS, and SECSII/GEM
- Development of industry standards such as MTConnect and Computer Aided Manufacturing using XML (CAMX)
- Coming soon to AMPF: 5G and future G technologies for ultra-fast connectivity
- Coming soon to AMPF: Millimeter wave (mmWave) technology for high-frequency data transmission
Extended Reality
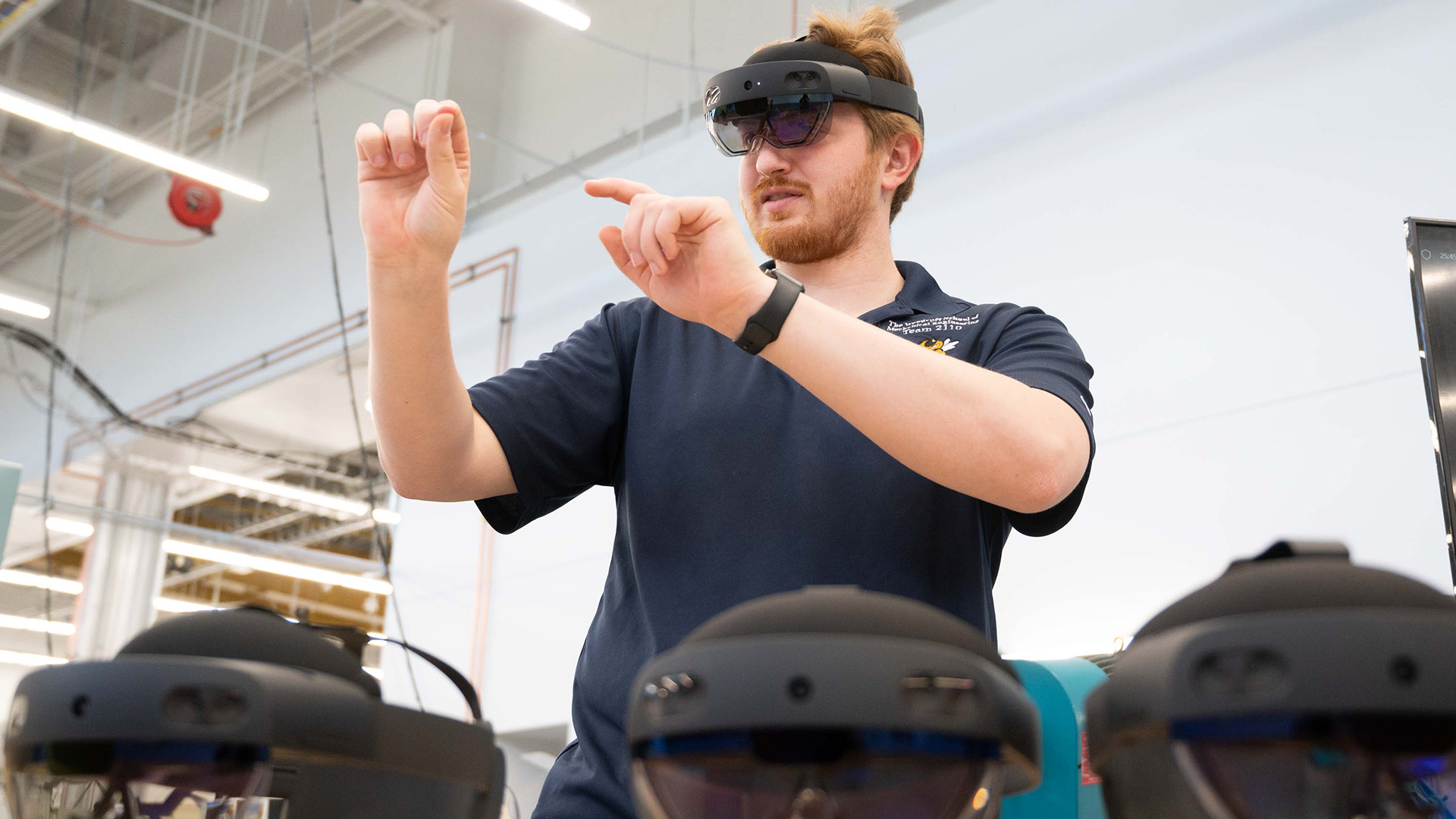
Coming Soon
In collaboration with the H. Milton Stewart School of Industrial and Systems Engineering, we are pioneering the use of extended reality (XR) technologies for product and workforce development. Our XR maker space will be dedicated to training, demonstration, and the development of augmented, virtual, and mixed reality applications.
Main Capabilities:
- Augmented Reality (AR) for overlaying digital information onto the physical world
- Virtual Reality (VR) for immersive simulations and training
- Mixed Reality (MR) for interactive experiences combining physical and digital elements
- Extended Reality (XR) encompassing AR, VR, and MR for comprehensive digital solutions
AMPF and Digital Capabilities Expansion
The AMPF is expanding into a 65,000+ sq. ft. facility, cementing its role as the nation’s premier advanced manufacturing innovation hub. This next-gen space will allow companies to pilot cybersecure smart factories, AI-enhanced robotics, and real-time process optimization, bridging the gap between research and real-world impact. With reconfigurable, digitally integrated, automated test tracks, the new AMPF will house the country’s first AI materials and manufacturing R&D facility. Capable of autonomous scale-up and real-time translation of research into practice, it will redefine academic-industry partnerships by accelerating commercialization and enabling agile responses to evolving manufacturing needs.